Advanced Techniques in Metal Stamping for Accuracy Production
As sectors consistently demand better tolerances and complex designs in their metal parts, the mission for innovative techniques in metal marking has actually heightened. From the application of sophisticated multi-stage stamping procedures to the assimilation of cutting-edge automation technologies, the landscape of metal marking is undertaking an extensive transformation.
Advanced Multi-Stage Stamping Processes
Going over the ins and outs of innovative multi-stage marking processes reveals the sophisticated methods utilized in contemporary production methods. Metal Stamping. Multi-stage marking is an intricate procedure that entails numerous actions to change a level sheet of steel into a final stamped product. The use of progressive dies, where different operations are performed at each stage of the stamping procedure, enables high accuracy and performance in the production of complex steel parts
During the initial stages of multi-stage marking, the level steel sheet is fed right into the stamping press, where a series of dies are made use of to reduce and form the material. Subsequent phases entail added developing, bending, and punching operations to more improve the component. Each stage is carefully designed to build on the previous one, bring about the production of complicated geometries with tight tolerances.
Advanced multi-stage marking processes require a high degree of knowledge and precision to make certain the top quality and consistency of the stamped components. By utilizing sophisticated machinery and tooling, producers can generate a wide variety of metal elements with effectiveness and accuracy.
Precision Tooling Innovations
Accuracy tooling technologies have transformed the steel stamping industry, improving efficiency and top quality in producing processes. These improvements have dramatically affected the way steel components are created, leading to greater precision and uniformity in the final products. One vital advancement is the development of computer mathematical control (CNC) innovation in tooling layout and fabrication. CNC systems enable elaborate layouts to be translated straight into tooling, making sure accuracy and repeatability in the stamping procedure.
Furthermore, the integration of sensing units and real-time surveillance capabilities in accuracy tooling has actually made it possible for suppliers to spot and attend to concerns promptly, reducing downtime and decreasing scrap rates. By integrating wise innovation into tooling, operators can enhance specifications such as pressure, speed, and alignment during the stamping operation, resulting in enhanced product quality and enhanced performance.
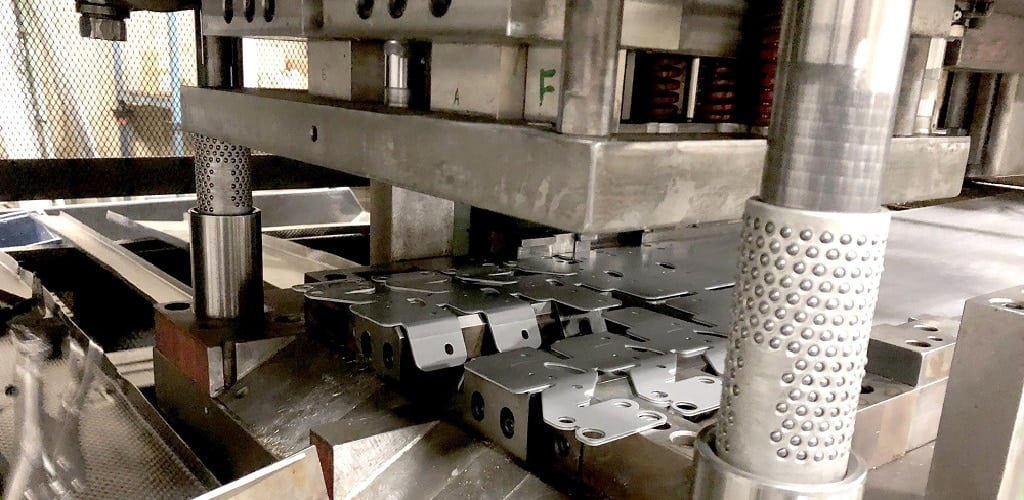
Automation in Steel Stamping
The evolution of accuracy tooling advancements in the metal stamping sector has actually led the way for considerable improvements in automation, changing the manufacturing landscape towards enhanced efficiency and performance. Metal Stamping. Automation in steel stamping involves making use of innovative equipment and robotics to carry out various jobs generally executed by human operators. This change in the direction of automation provides numerous advantages, consisting of improved precision, quicker production cycles, and lowered labor expenses
One key facet of automation in steel stamping is the execution of computer mathematical control (CNC) systems, which allow accurate control over the marking process. CNC modern technology permits the creation of facility and elaborate steel get rid of consistent high quality. Additionally, automated systems can be set to run continuously, bring about higher result rates and much shorter lead times.
In addition, automation improves office safety by lowering manual YOURURL.com handling of hefty products and reducing the threat of accidents (Metal Stamping). As producing sectors continue to welcome automation, the future of steel stamping holds excellent promise for also better efficiency and advancement
High-Speed Stamping Techniques

Among the key benefits of high-speed marking strategies is the ability to produce a large volume of parts in a much shorter quantity of time contrasted to typical why not try this out marking approaches. This increased productivity not only allows manufacturers to fulfill limited manufacturing target dates however likewise allows expense savings through economies of scale. In addition, high-speed marking can aid minimize material waste by optimizing the material use throughout the stamping process.
Furthermore, high-speed marking strategies commonly integrate ingenious features such as fast die adjustment systems and real-time tracking capabilities, further boosting the general effectiveness and flexibility of the steel stamping process. As modern technology proceeds to advancement, high-speed marking is anticipated to play a vital role in driving the future of accuracy production.
Quality Assurance in Stamping Procedures
Efficient quality control actions are go now necessary for guaranteeing the reliability and uniformity of metal marking operations. Quality assurance in marking operations entails a series of organized processes intended at discovering and preventing issues in the produced parts. One important facet of quality assurance in steel stamping is the usage of advanced assessment techniques such as optical assessment systems and coordinate measuring makers (CMMs) to validate the dimensions and resistances of stamped components.
Furthermore, quality assurance measures in stamping procedures frequently consist of the execution of statistical process control (SPC) approaches to monitor the production procedure in real-time and ensure that it continues to be within acceptable limitations. By evaluating data and recognizing fads, makers can proactively address any kind of inconsistencies from the wanted quality requirements.
Additionally, high quality control in steel stamping operations also includes thorough product testing to make certain that the raw materials utilized meet the called for specs for the stamping process. This may consist of carrying out material hardness examinations, tensile strength examinations, and dimensional assessments to ensure the quality and stability of the stamped elements. On the whole, carrying out robust quality control procedures is critical for achieving high-quality stamped parts constantly.
Verdict
To conclude, advanced techniques in steel stamping play an important function in accuracy manufacturing processes. Through multi-stage marking processes, ingenious tooling solutions, automation, high-speed strategies, and strenuous top quality control measures, suppliers can achieve greater degrees of accuracy and effectiveness in their operations. These developments in metal stamping technology have made it possible for companies to generate complicated get rid of tight resistances, inevitably leading to boosted product top quality and consumer complete satisfaction in the manufacturing sector.